OxygenExtreme conditions - Safe solutions
With increasing pressures and/or temperatures in oxygen applications, the risk of fire also increases.
Due to the fire-promoting effect of oxygen, the ignition temperature of materials is significantly reduced. As a result, materials that are not flammable under normal ambient conditions are now completely burnt under the effect of the oxygen.
At high pressures, pressure surges can cause very high temperatures. These significantly exceed the ignition temperature of metallic materials, which is lower under the influence of oxygen, which can lead to catastrophic fires.
Goetze is your partner in safety here too.
For critical applications of this kind, GOETZE has developed a suitable and safe solution with the series 492GOX. The pressure-bearing parts here have been replaced by correspondingly safe materials such as Monel and brass.
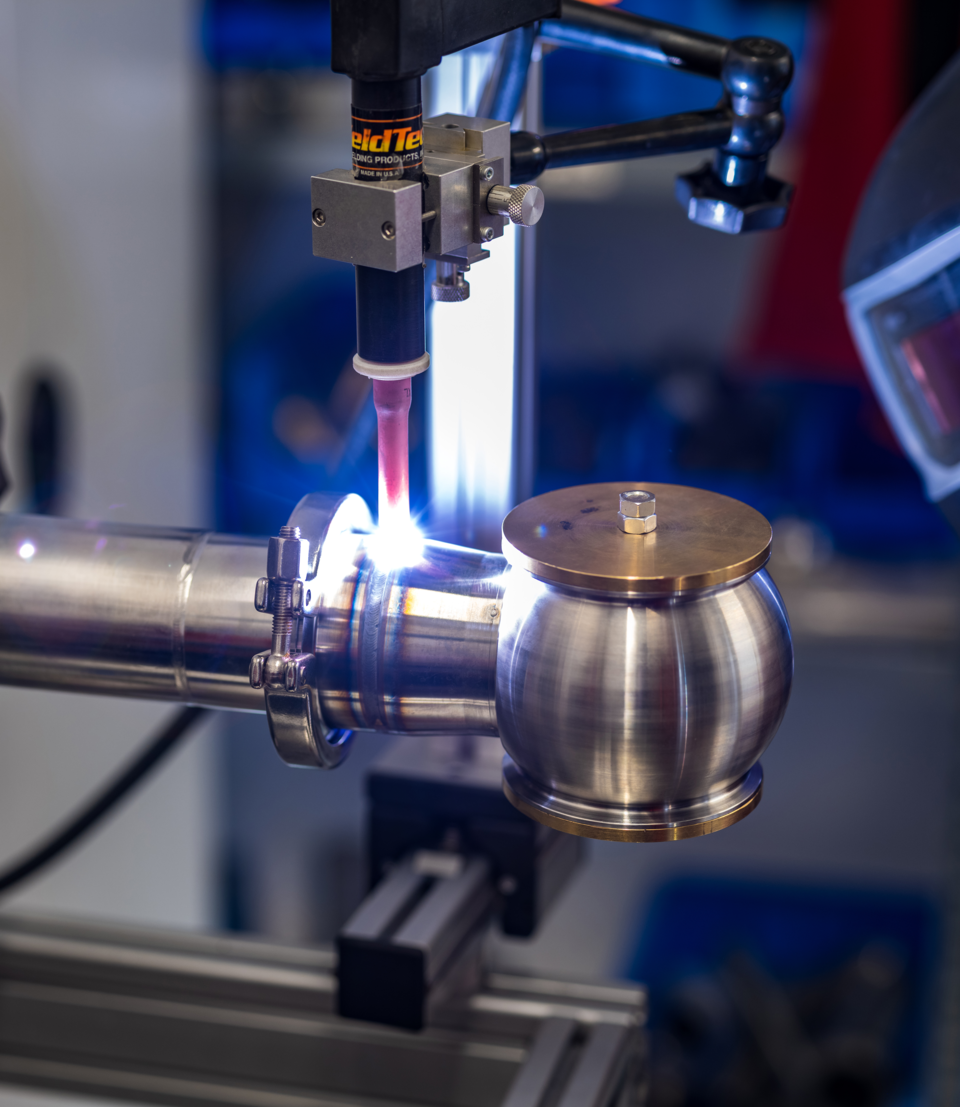
APPLICATIONS WITH OXYGEN? BUT SAFE! Oxygen valves in use
Safety valves that are specially designed for oxygen applications are used in a wide variety of industries. In particular, in the area of the production of technical gases, medical gases, with compressor manufacturers as well as component manufacturers and plant constructors.
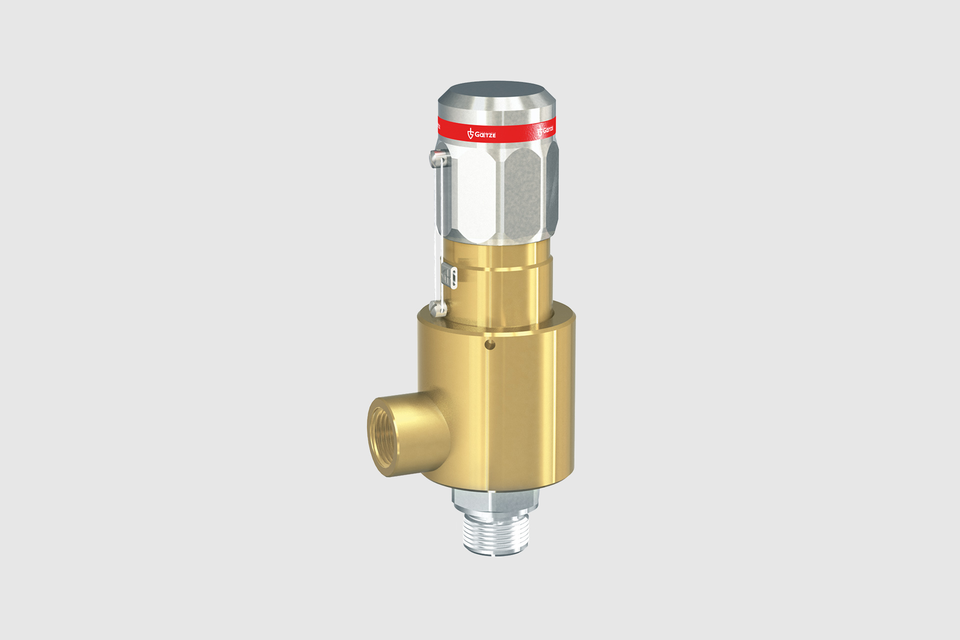
Due to the special requirements for high-pressure oxygen, the 492GOX safety valve has components made of Monel to safely prevent oxygen burnout.
In addition, the 492GOX safety valve was subjected to a special oxygen pressure surge test.
EXTREME CONDITIONS - SAFE SOLUTIONSProduction process Purified Gases
The handling of high-purity gases requires extreme care throughout the entire production process.
In the area of oxygen applications, it is necessary to use sealing materials that have been tested by the Federal Institute for Materials Testing (BAM) for the area of application:
- Cleaning of the individual parts with specific solvents and ultrasound. The individual parts are then packed in closed transport boxes.
- The assembly, testing, packaging and labelling of the valves is carried out at our own assembly stations. These steps serve the purpose of achieving corresponding limit values of hydrocarbon compounds and particle impurities.
- Dispatch of the valves to the customer.
Professionally trained personnel, compliance with all relevant regulations and recurring processes, monitoring of the cleaning which is free of oil, grease and particles, assembly, testing, packaging and labelling guarantee customers a valve which conforms to high-purity gas standards for their applications.
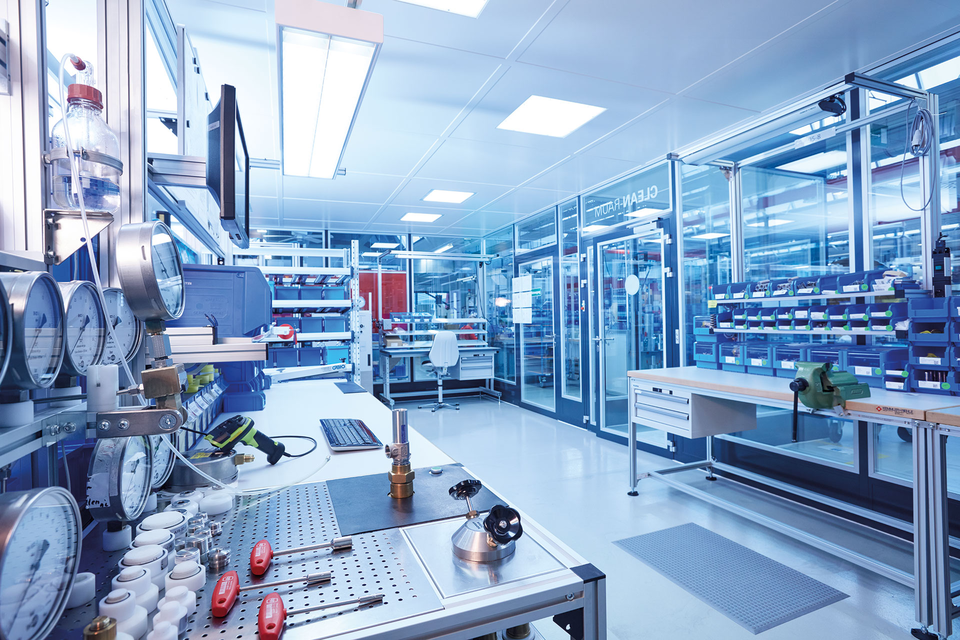
Reading materialExtreme conditions - Safe solutions
Read our brochure on the subject of technical gases.